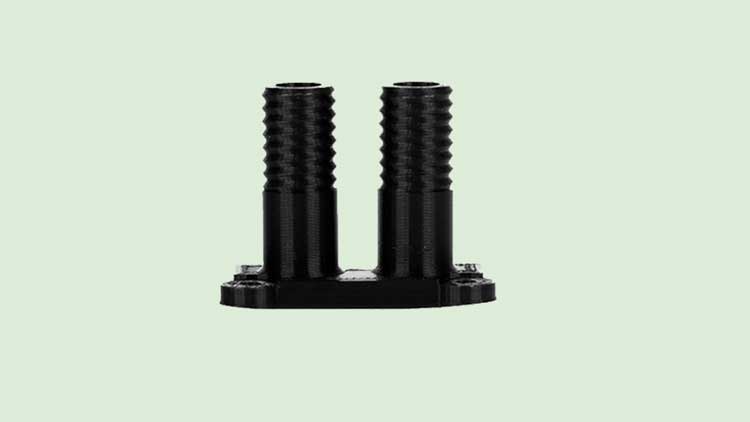
ABS, also referred to as Acrylonitrile Butadiene Styrene, is a thermoplastic that can be used as filament for 3D printers. Its properties as a thermoplastic include the ability to change from a solid state to one that is soft and moldable when heated, and back again when cooled. ABS is made of petroleum, which explains why it has a strong, pungent plastic smell when heated. Before any colors are added, it is naturally beige.
ABS must successfully complete three tests before it may be utilized as a filament for additive manufacturing. It needs to be turned into a plastic filament first. Second, during the printing process, it must undergo a second extrusion and trace-binding. Finally, it must successfully implement its intended end use. ABS is noted for possessing strength, flexibility, machinability, and a stronger temperature resistance than PLA. It passes all three tests.
Strong and just slightly flexible, ABS has a propensity to bend rather than break. It is easily sanded and machined. It is well recognized for being used to make LegosTM. At 90°C, it begins to soften; at 180°C, it melts; and at 230°C, it firmly binds.Hydrophilic is a term used to describe ABS. ABS will bubble and erupt out the tip of the 3D printer nozzle when it is exposed to moisture for an extended period of time, such as humidity.
ABS demands a hot printing platform for a successful 3D print. Additionally, it is advised to keep the room at a comfortable temperature or to place the printer inside a small warm space. This goal can be achieved by covering the printer with a box of cardboard during printing. ABS is vulnerable to bottom warping, curling, and splitting if the aforementioned safety measures are not taken, as well as a level platform.