A semi-crystalline thermoplastic with the abbreviation PEKK, or polyetherketoneketone, is utilized more frequently in the additive manufacturing industry. It is frequently compared to PEEK and is a member of the same PAEK family, which is renowned for its mechanical and chemical qualities. PEKK is more readily available in the form of filament suitable with high temperature machines than PEEK, which makes it easier to print, especially given its slower rate of crystallization. It is also available in powder form for a very small number of SLS 3D printers. It is still an extremely expensive and technically complex material, primarily utilized in demanding industries like aerospace or oil & gas. What features does PEKK have in 3D printing, then?
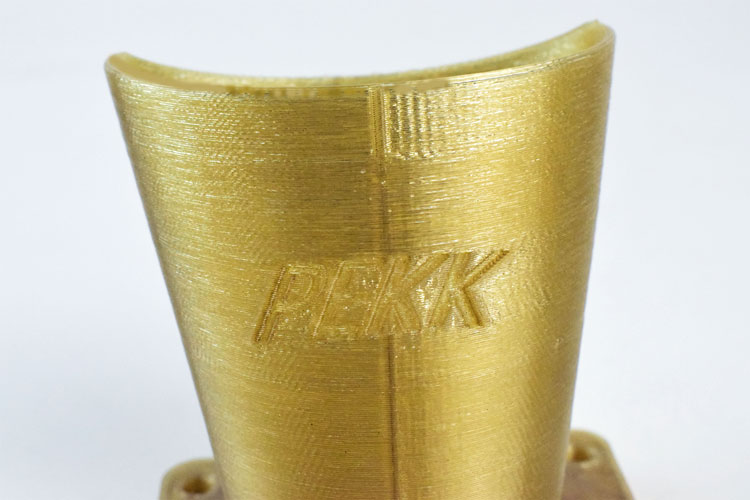
Its basic ingredients, ketone and ether, are remarkably similar to those of PEEK. The ratio of ether to ketone in PEKK is higher, and ketone bonds are more flexible than ether bonds. This is the major distinction between these two high-performance materials. In particular, this makes the polymer chains more stiff, which raises the melting and glass transition temperatures (the temperatures at which the polymer begins to soften). Furthermore take note that there are other variations besides this ratio. In fact, it is feasible to alter the melting point and the rate of crystallization by changing the position of the ketone bonds in the aromatic ring.
In more literal terms, PEKK can be thought of as an amorphous polymer because it crystallizes at a slower rate. It won’t be as influenced by cooling, giving it better adhesion to the tray and preventing warping. It is therefore simpler to print than PEEK. Moreover, it has better wear and friction characteristics and a better aesthetic look.
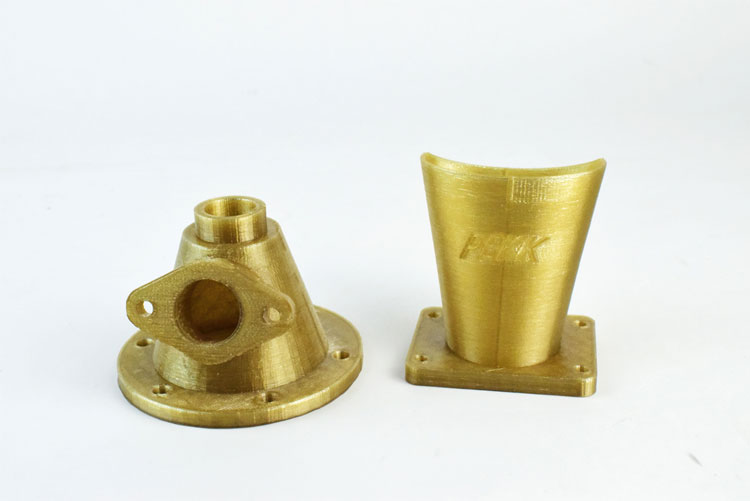
PEKK has excellent resistance to chemical and abrasive aggressiveness. In reality, it can withstand a wide range of liquids, including numerous alcohols and benzene, the refrigerant used in the car industry. Also, the substance possesses excellent insulating and dielectric stability, both of which are advantages in the electronics industry. Finally, PEKK has no harmful emissions and is not combustible. PEKK has extrusion temperatures that typically range from 340 to 360 °C and will require both a heated chamber and plate for printing purposes. With the exception of a slightly lower extruder temperature, the criteria are nearly identical to those for PEEK.
Because of its resistance to pressure and high temperatures, PEKK is widely used in the oil and gas industry as well as the aerospace and automotive industries. The material’s excellent weight to strength ratio makes it the perfect choice for manufacturing important parts in the aerospace industry, where lowering weight is essential to maximizing performance. The rigidity and lightness of PEKK can also be increased by using carbon fiber reinforcement.