Short fiber reinforced polymer composite parts have been successfully created using fused deposition modeling (FDM). Due to the inherent mechanical property constraints of matrix polymers, it is urgently necessary to create fiber-reinforced high-performance thermoplastic composites for FDM-3D printing in order to broaden engineering applications. What are the potential differences between short carbon fiber (CF) and glass fiber (GF) reinforced high performance PEEK composites produced using FDM-3D printing? Microscopical morphological analysis was used to describe it, and thermal performance testing revealed that it has superior thermal stability than pure PEEK. Focus was placed on evaluating the mechanical properties, microstructure, surface quality, and porosity of the printed CF/GF-PEEK pieces.
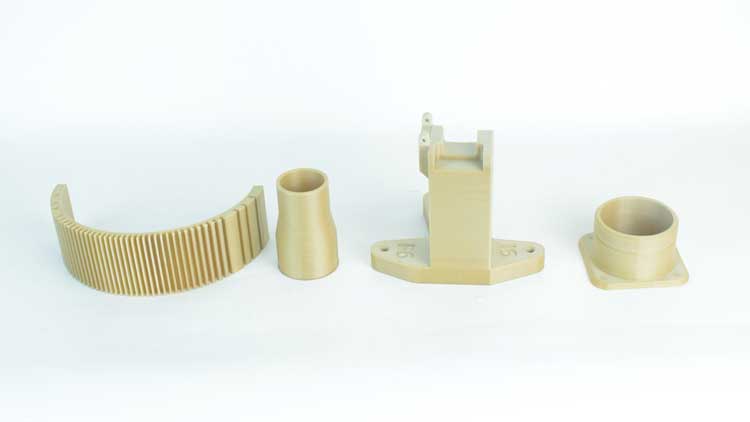
The findings demonstrate that the tensile and flexural strengths of PEEK can be greatly increased by the addition of CF/GF at the expense of ductility. To enhance the printed CF/GF-mechanical PEEK’s characteristics, surface quality, and porosity, a lower fiber concentration of 5 wt% is advantageous. Due to differing fiber surface treatments, GF/PEEK and CF/PEEK have greater interfacial bonding. Moreover, microstructural examinations showed that in 3D printed CF/GF-PEEK, holes would result in performance reduction whereas fibers aligned along the printing direction could improve performance.
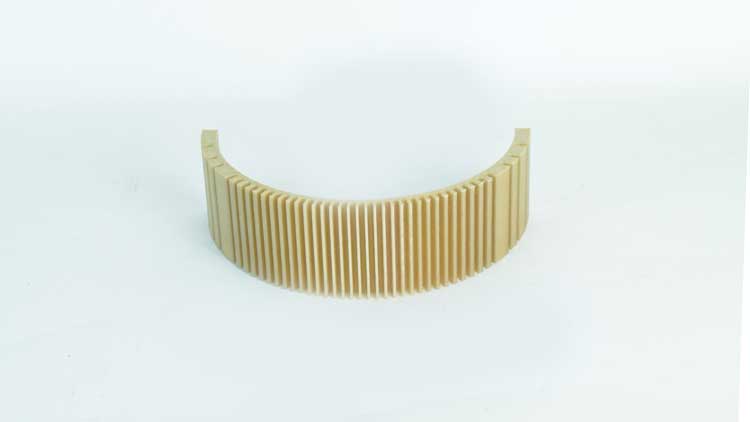
due to PEEK materials’ high melting temperature and high viscosity, which make it difficult to generate filaments for FDM-3D printing. Glass fiber has a different aspect ratio, surface structure, and mechanical properties than short carbon fiber.
In conclusion, the goal of this work is to investigate the possibility of FDM-3D printing short fiber reinforced PEEK composites for engineering applications. In order to successfully meet various production requirements, this effort aims to provide a quick prototyping solution for difficult shape, high-strength, and lightweight applications.