A New Choice For Aerospace Manufacture
When developing new aerospace product, cost and risk comes by. Designers need to ensure they will work on the first implementation. IEMAI 3D printing provide aerospace manufacturing a flexible prototyping to iterate generously and with no error. With 3D printing, designers will be able to design more complicated model which reduced the weight of parts and at the same time maintain its performance.
Lightweight is one of the most representative of 3D printing materials. Using the same design, the 3D printed parts can be half or even a quarter of the original weight. This reduces the material costs spend on parts and at the same time also reduces the cost spend on fuel.
For example, according to the 2016 Global 3D Printing Report, Airbus A350 XWB has over 1000 3D printed parts, saving 25% of fuel.
Due to the simplicity in operation of IEMAI 3D printer, you will open a new era in aerospace industry, you can produce factory tooling in-house-massively reducing product development costs and lead times and not to worry about your supply chain anymore.
With 3D printing, engineers and designers can freely explore more complex design for parts that can provide the highest performance; no longer limited by most traditional manufacturing methods. Aerospace companies can rethink how a component should be implemented and developed through rapid prototyping, testing, and verifying these assumptions.
The additive manufacturing process of 3D printer technology (layer-by-layer deposition of materials) allows the designer to merge multiple parts into a single functional part in modelling software. This means that with the simplified assembly, the operating and processing cost are reduced.
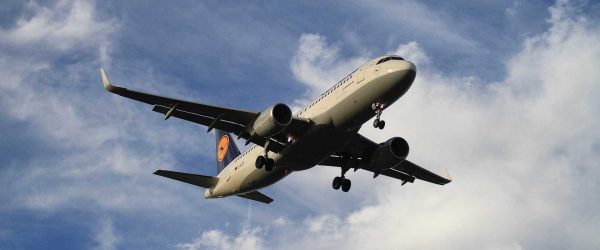
Commonly Used Printers
Commonly Used Materials
Trusted Globally By
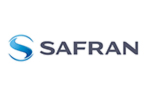
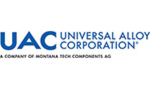
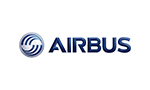